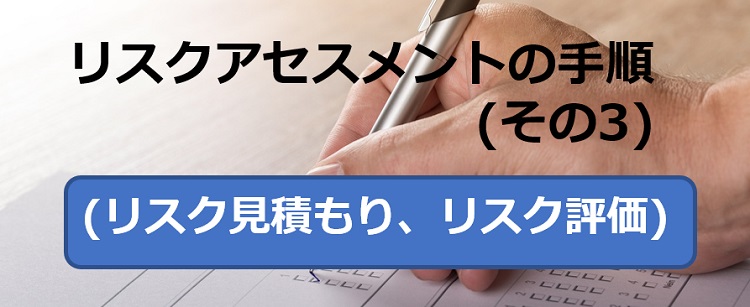
前回コラムでは、リスクアセスメント(Risk assessment)の見積りについてお話しましたが、今回はその続きとなります。
下記関連コラムも合わせてご覧ください。
リスクの見積り(続き)
機械指令(2006/42/EC)、及びEN/ISO 12100におけるリスクの見積りにつきましては、具体的に決まった手法は明示されていません。
しかしながら、リスク見積りのプロセスを支援する為に開発された下記に挙げるリスク見積りツールを適切に選択し、使用する事で目的に合ったリスクアセスメントが可能になります。
リスクの見積りツールの例は、ISO/TR 14121-2というリスクアセスメントの手引き及び方法例が示されたテクニカルレポート(技術報告書)文書に挙げられています。
この規格で挙げられている主なリスク見積りのツールは以下の通りです。
(a) リスクマトリックス
(b) リスクグラフ
(c) 数値採点法
これらのツールについて、ご紹介していきたいと思います。
まず、ツールの使用における共通概念として、リスク見積りツールは、リスクの要素を代表する少なくとも2つのパラメータを取り扱う事が必要となります。
これは前回のコラムでリスクの定義として記載致しました、“危害のひどさ”と“危害の発生確立”になります。
これら2つのパラメータを組み合わせて、リスクの見積りを行う事となります。
それではひとつずつ見ていきましょう。
(a) リスクマトリックス法
まず、(a)のリスクマトリックス法とは、“危害のひどさ”と“危害の発生確立”を下記のようなテーブルに配置し、行と列が交差する部分をリスクレベルとする方法となります。
リスクマトリックス法の場合、以下の様なテーブルが一般的に使用されています。
危害のひどさ (特に重大) |
危害のひどさ (重大) |
危害のひどさ (中程度) |
危害のひどさ (軽微) | |
---|---|---|---|---|
発生確率 (非常に高い) |
高 |
高 |
高 |
中 |
発生確率 (高い) |
高 |
高 |
中 |
低 |
発生確率 (低い) |
高 |
中 |
低 |
わずか |
発生確率 (非常に低い) |
低 |
低 |
低 |
わずか |
汎用的に使用されるのは、このような2次元のテーブルとなりますが、危害の発生確率を「危険源への暴露頻度」、「危険事象の発生確率」及び「危害の回避の可能性」といった3つのパラメータに分け、最大4次元までのテーブルとすることも可能です。
ISO/TR 14121-2では、リスクマトリックス法を用いたリスク見積りは、簡易的であり、かつ効果的な方法であるとされています。
(b) リスクグラフ法
続いて、(b)のリスクグラフ法ですが、リスクグラフ法はリスクの要素を4つのパラメータ「危害のひどさ」、「危険源への曝露頻度」、「危険事象の発生確率」、「危険回避の可能性」に分けて決定し、分析に基づきリスクの見積もりを行う手法です。
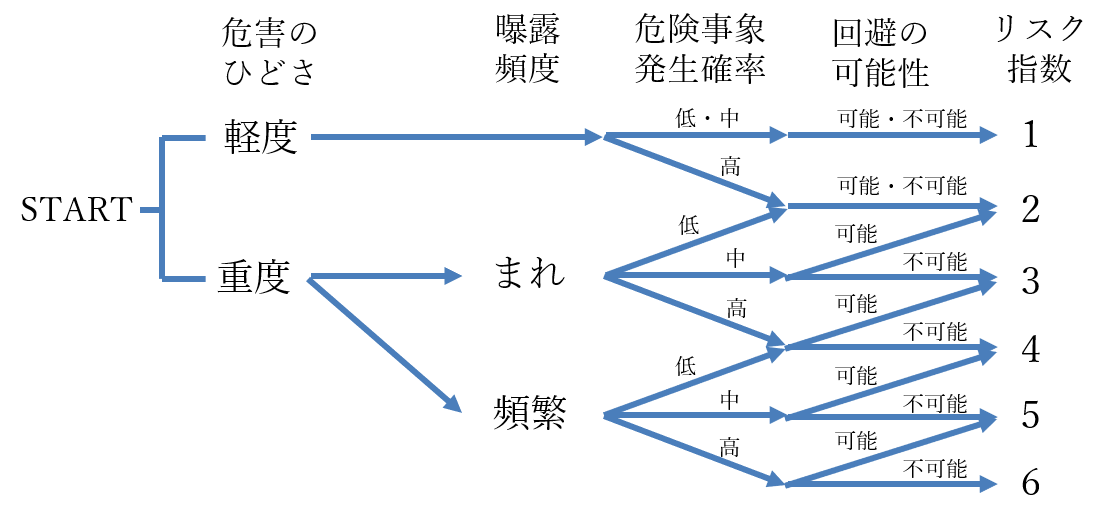
このリスクグラフ法は、一般的に急性プロセスの危害(危険事象発生時に直ちに起こる危害:機械的、電気的等)に対するリスクの使用に適しています。
しかし、騒音や振動、人間工学といった慢性的(長期的)に発生するような危害に対しては適していません。
(c) 数値採点法
最後に(c)の数値採点法ですが、前述のリスクマトリックス法やリスクグラフ法と同じように、2つ以上のパラメータを用います。
リスクマトリックス法やリスクグラフ法は、パラメータが定性的なものであったのに対し、数値採点法では、各パラメータに点数を割り当て、値の組み合わせ(加算や乗算等)によりリスクレベルを決定する方法です。
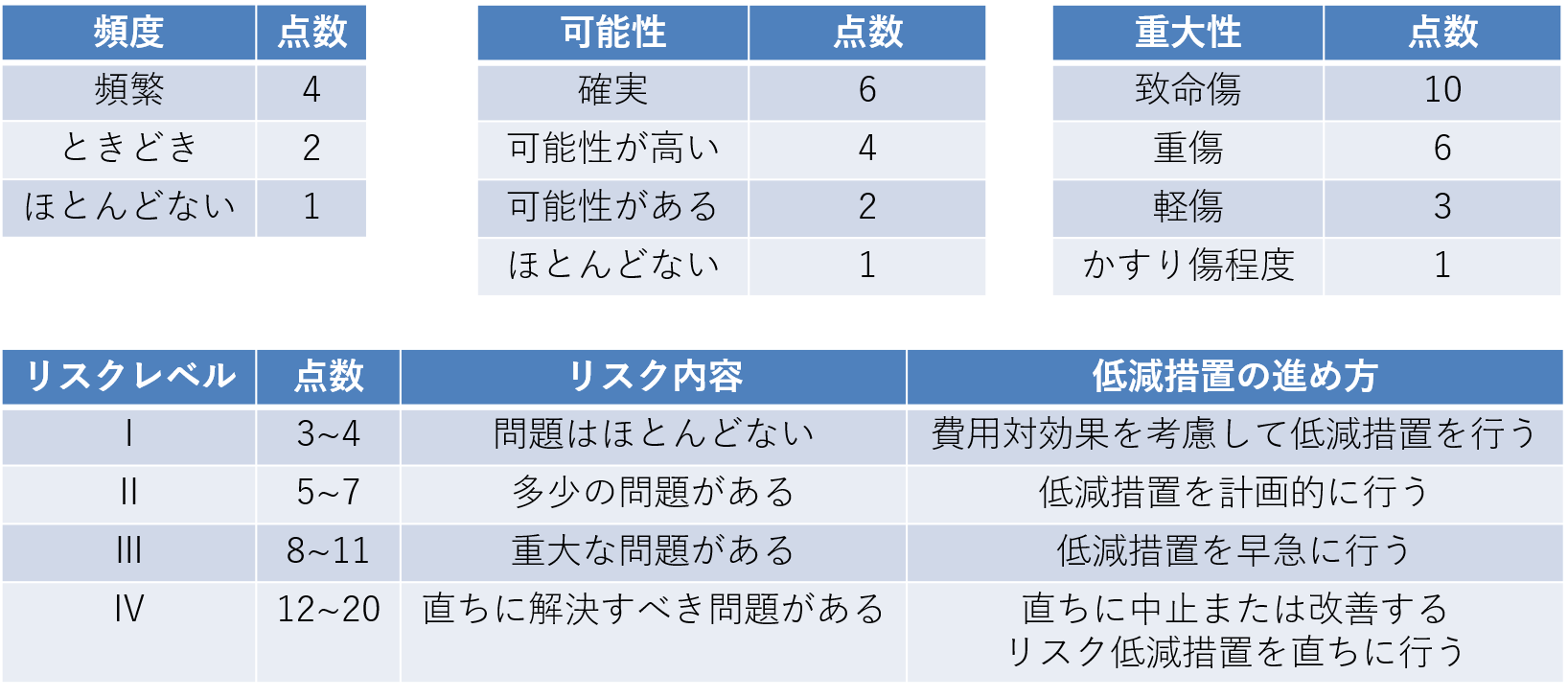
数値採点法は、数字を使用する事により、定性的なものを定量化することにより、より詳細な選択が可能となりますが、使用する数値や組み合わせの精度により、適切なものとはならない可能性もありますので、注意が必要となります。
このようなリスク見積もりのツールを適切に使い、リスク見積もりを行います。
リスク評価
それでは、次のステップの「リスク評価」に関する内容に入っていきます。
リスク評価では、見積もったリスクが適切に低減されているかどうかの確認を行います。
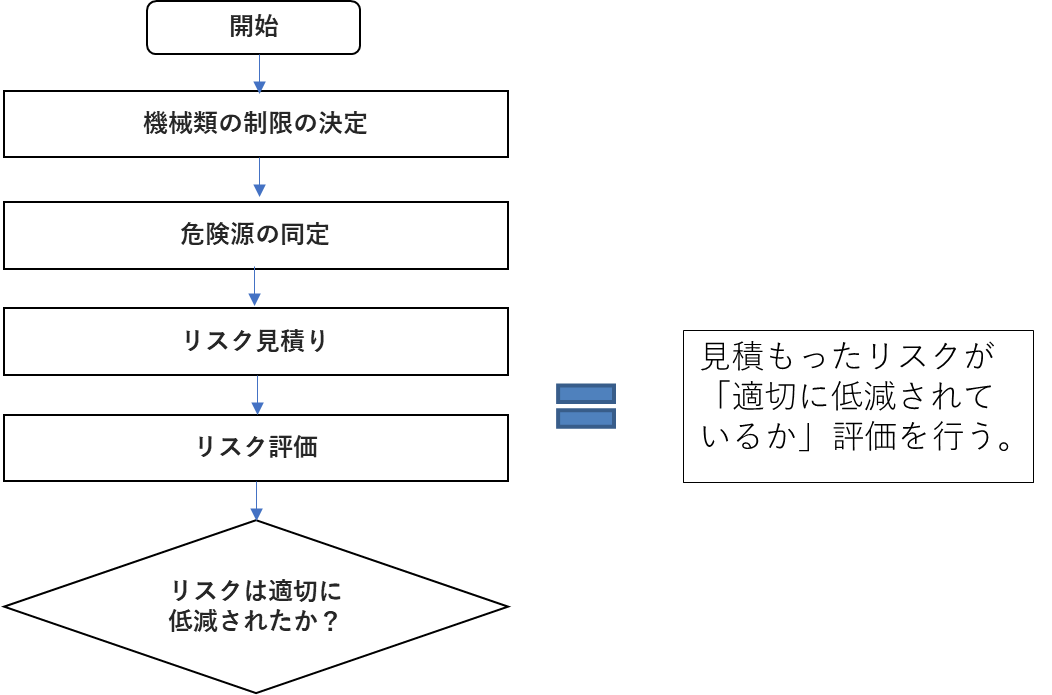
リスク評価の目的は次の通りです。
- どのような危険状態におかれることで、更なるリスク低減が必要となるのかを決定するため。
- 必要なリスク低減が更なる危険源を誘発する事無く、または、他のリスクを増加させる事無く達成されたかを判定するため。
リスク評価の結果、リスクが適切に低減されていると判断出来れば、その結果をリスクアセスメントシートにまとめ、文書化し、リスクアセスメント作業は終了となりますが、見積もったリスクが適切に低減されていないという結果となった場合、一体どうすればよいでしょうか。
当然ながら、この場合は「リスク低減」という作業が必要となります。
リスク低減とは
リスク低減は、危険源そのものを除去するか、またはリスクを決定するための2つの要素である「危害のひどさ」及び「危害の発生確率」を低減する事によって達成可能となります。
ISO 12100において、リスク目的を達成するための全ての保護方策は、“3ステップメソッド”に基づき、次の順序で適用する事が要求されています。
<3ステップメソッド>
ステップ 1:本質的安全設計方策
機械自体、または機械と曝露される人との間の相互作用に関する設計特性を適切に選択することにより、危険源を除去するか、またはリスクを低減する。
ステップ 2:安全防護策/付加保護方策
危険源を除去、またはリスクを十分に低減することが本質的安全設計方策で実施不可能である場合、意図する使用方法、及び合理的に予見可能な誤使用を考慮した上で、適切に選択した安全防護、及び付加保護方策を講じることにより、リスクを低減する。
ステップ 3:使用上の情報
本質的安全設計方策、安全防護及び付加保護方策の採用にもかかわらず、リスクを十分に低減できない場合、使用上の情報で残留リスクが認識されなければならない。
使用上の情報には次を含まなければならないが、これに限定しない。
− 使用する人又は危険源に暴露されるその他の人の予想される能力に応じた機械類の操作手順
− 推奨される安全作業要領及び訓練の要求事項
− 残留リスクに関する警告を含む、機械類の寿命の様々な局面に対する十分な情報
− その必要性及びその使用に必要な訓練要求事項を含む、推奨される個人用保護具の詳細
本質的安全設計方策、安全防護又は付加保護方策を適切に適用するところを使用上の情報で代替してはならない。
(JIS B 9700より)
このように、リスク低減では、3ステップメソッドのステップ1として、「本質的安全設計方策」を考えます。
まずは危険源自体をなくすことができないかどうか、本質的な部分から考慮します。
それが製品機能や仕様に影響を与えるために困難である場合は、次のステップ2である「安全防護策/付加保護方策」を考えていくことになります。
ここでは、ステップ1で考慮した危険源に対し、ガードや保護装置を付けるなどの安全防護ができるかどうかを検討します。
さらに、付加保護方策として、非常停止装置を付けるといったことを考えていきます。
そして、最後のステップ3である「使用上の情報」では、警告ラベルやマニュアルへの注意喚起といった内容を考えていく必要があります。
次回は、「リスク低減の3ステップメソッド」について、もう少し詳しいご説明をしていきたいと思います。
当社では、お客様製品のリスクアセスメントの実施、リスクアセスメントシートの作成支援等を行っておりますので、お気軽にご相談頂ければと思います。
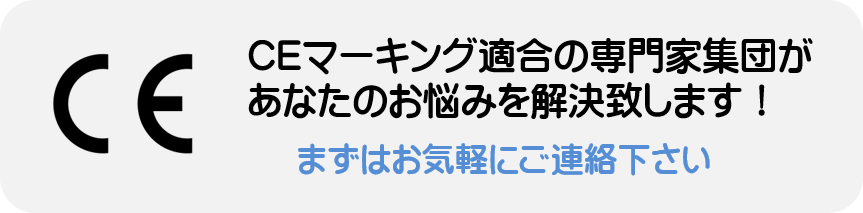