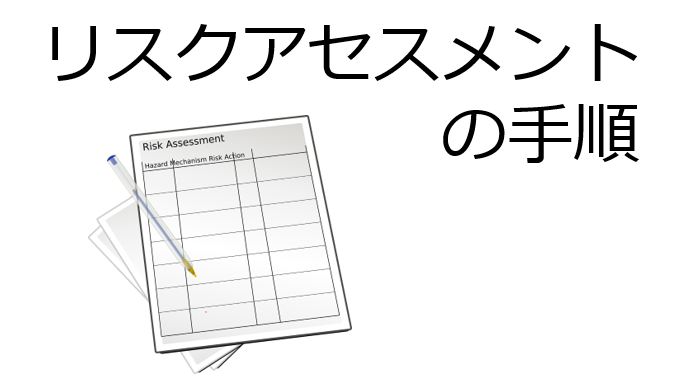
前回コラム「リスクアセスメントの実施」に引き続き、今回は具体的なリスクアセスメント(Risk assessment)の手順に入っていきたいと思います。
まず、リスクアセスメントの中でも非常に重要となる「使用上の制限手順」、「危険源の同定」について考えていきたいと思います。
リスクアセスメントの手順 (1.資料集め ~ 3.危険源の同定)
リスクアセスメントの手順に入っていく前に、注意しておきたいことがあります。
それは、製品のライフサイクルの全局面の安全性を考慮するということです。
要するに、製品の運搬、据付け/設置段階から解体、廃棄に渡るまで、製品の一連のライフサイクルでリスク査定を行うことが必要になります。
例えば、運搬時におけるリスクとして、構成部品が落下して、運搬業者が挟まれる可能性がある、といったように、それぞれの局面で考えられるリスクを、リスクアセスメントで考慮しておかなければなりません。
リスクアセスメントでよく見受けられることとして、ユーザーの通常使用や保守に関するリスクばかりが取り上げられがちですが、例えば、運搬や廃棄時といったリスクが抜けているものがよくありますので、この点についても注意が必要となります。
それでは、次のフローに沿って説明を行っていきます。
細かい部分は省略していますが、リスクアセスメントは、フロー図にある手順に基づき、進めていきます。
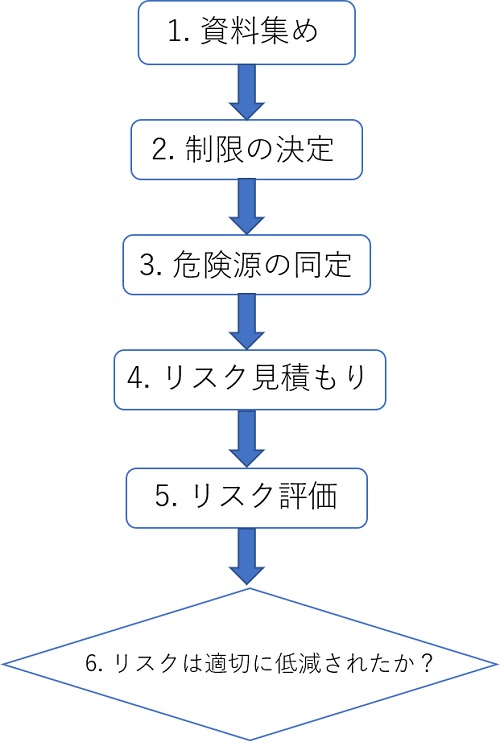
1. 資料集め
リスクアセスメントを実施する場合、特に製造メーカーの方々は対象製品のプロフェッショナルですので、どうしても自らの感覚や経験のみを基に進めてしまう時があります。
しかし、製品事故の大多数は、技術者の感覚や経験を超えた原因により発生しているというのも事実です。
その為、リスクアセスメントを行う為の材料となる資料類をまず収集しておきましょう。
これには、製品ユーザーの想定仕様や製品そのものの仕様、関連する法規制や機械の事故事例等が当てはまります。
また、製品が設計段階の場合、類似機種の資料等が大いに役立つ事もあります。
2. 制限の決定
リスクアセスメントは、製品の寿命、ライフサイクルにおける全ての段階を考慮した制限の仕様を決定する事が必要となります。
製品性能、特徴、その製品に関わる人、その人の特性等、様々な点を考慮して、どこまでの内容を想定するのか、について決定しておかなければ、リスクアセスメントを行う範疇が定まらず、ゴールまでたどり着けません。
この制限の決定は、非常に重要になります。
(EN) ISO 12100では、制限の決定について、大まかに以下の3つの項目に分けています。
- 使用上の制限
- 空間上の制限
- 時間上の制限
この限りではありませんが、それぞれ以下の様な内容を制限として予め決定しておきます。
使用上の制限とは?
機械製品を例に挙げた場合のものです。下記の表をご覧ください。
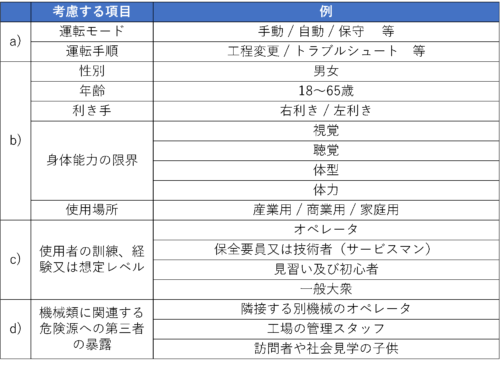
表 1.(使用上の制限)
使用上の制限で気を付ければならないのが、機械で怪我をする人はその機械製品の使用者だけには限らないということです。
通常、工場で使用する機械であれば、対象機械の隣に機械が置かれているケースも大いにあり得ます。
機械のオペレータなら、明らかに認識している危険な部分であっても、隣の機械のオペレータがたまたまその部分に触って怪我をするという可能性もあり得るわけです。
場合によっては、工場には作業者以外の方、掃除をしている方や社会見学に来た子供、といった可能性もあるかもしれません。
あくまでこれらは一例であり、合理的に予見可能な場合はこれらの内容も含み、アセスメントを行う必要があります。
もちろんこれは、絶対あり得ないといった事までは考慮する必要はありません。
“合理的に予見可能かどうか” が重要となります。
2006年、シュレッダーで指を切断したという大きな事故がありましたが、その事故の原点は、「合理的に予見可能かどうか」という点が考慮されていなかった事が大きな原因であると考えられます。
空間上の制限とは?
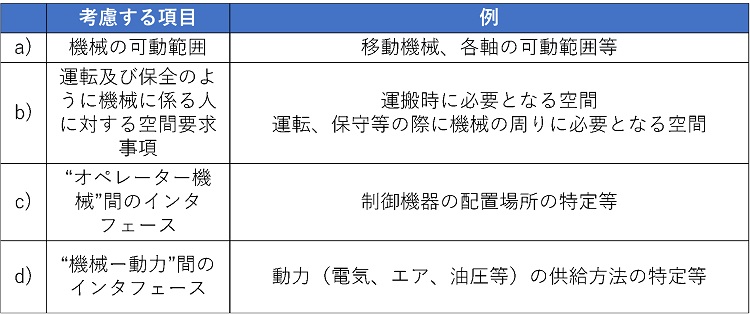
表2.(空間上の制限)
空間上の制限は、機械の周りの空間やインタフェース、操作機器類の位置を想定し、制限事項に加える事です。
これを決めておかないと極端なことを言えば、機械の周囲にスペースが無い状態で設置が行われ、十分な保守作業が実施出来ない可能性があります。
時間上の制限とは?
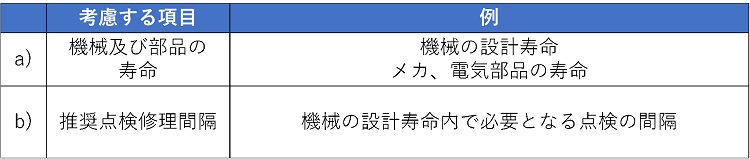
表3.(時間上の制限)
時間的制限とは、簡単に言えば機械そのものや構成部品の機械的、電気的寿命を特定しておきましょうということです。
これを特定しておかないと、例えば、構成部品の寿命内に部品交換が行われず、故障が発生したり、ドリルの交換作業についてのリスクアセスメントをしようとしても、その頻度が特定できないといった事が起こり得ます。
これら全ての制限事項に言える事として、機械の制限の決定を含むリスクアセスメントを行う際には通常の意図する使用方法だけではなく、合理的に予見可能な使用方法も考慮する必要があります。
この点について、詳細は後述致します。
このような制限の決定を行わずに、いきなりリスクアセスメントシートを作成しているケースがありますが、本来の手順の通り、機械の制限の決定を行った上で次の手順に移るということが重要なポイントです。
3. 危険源の同定
危険源の同定とは、危険源、危険状態及び危険事象を抽出する作業のことを指します。
要は、誰が何をしている時に、どのようなリスクがあるのか、ということについて考えていく作業になります。
この危険源の同定作業は、リスクアセスメントのプロセスにおいて、最も重要であるとされています。
危険源の同定の洗い出し作業で、一つでも抜けがあると、それが原因で危害に至る可能性がありますので、抜けること自体が許されません。
色々と事象を考慮した上で、全てのリスクを洗い出します。
それ故に、機械安全に精通した経験豊富なエンジニアによる製品リスクの抽出作業は、最も重要な作業です。
リスクの同定には、意図する使用と先程記載致しました合理的に予見可能な誤使用を考慮する必要があります。
機械の製造者側の立場で言えば、意図した使用の中で許容出来ないリスクがあっては当然いけませんので、意図する使用時における、危険源の同定を行います。
また、意図する使用では無いが、やってしまう可能性があるといった誤使用である合理的に予見可能な誤使用についても当然ながら考慮する必要があります。
通常は、機械ごとに定められた使用方法、意図する使用に基づき忠実に機械が使用されていれば、機械起因の事故はほぼ発生しないと考えられます。
現在の機械業界では、あらゆる場面で自動化が進んでおりますが、機械のライフサイクルの中で作業に人が介在しないような機械は有りません。
通常の運転は、全自動で行う様な機械でも、どうしてもメンテンナンス時には人の介入が必要となります。
幾ら真面目な作業者でも、人は必ず間違えます。
又、ルールを破る可能性のある人も一定の割合で存在しています。
そのような前提を踏まえた上で、リスクアセスメントを行うことが必須であり、その為に合理的に予見可能な誤使用を当然考慮する必要があるわけです。
もちろん、誰がどう判断しても絶対にあり得ないといった誤使用までは考慮不要です。
しかしながら、これも主観的な意見ではコンセンサスが欠けますので、様々な分野の方々を集約したチーム構成でのリスクアセスメントが有効ということに繋がります。
人間は皆、楽をしたいという気持ちは持っていると思います。
メーカが指定した使用方法より、簡単に早く出来る方法があれば、人はその様に作業を実行してしまいます。
例えば、通行禁止の場所であっても、そこを通った方が近ければ通ってしまう可能性があります。
数年前のことですが、首につけた防寒具が果物の洗浄装置に巻き込まれて、農家の方が亡くなったという悲痛なニュースがありました。
例えば、取扱説明書で首元に付ける防寒具の使用が禁止されていたとしても、果物の洗浄装置の使用において、秋から冬場に掛けて収穫する屋外の作業で、使用中に防寒具を着用している事が、予見可能では無かったのかと考えてみると疑念が残ります。
日本国内においても無過失責任における機械事故の判例がある様に、製造者側は誤使用に対しては、特に気をつかってリスクアセスメントを行う必要があると言えます。
今回はここまでにします。
続きは、次回コラム「リスクアセスメントの手順(2)」でご紹介させて頂きます。
イーエムテクノロジーでは、リスクアセスメントのやり方はもちろん、法規制の解釈や、リスクアセスメントシートの作成、注意点等を相談しながら、お客様と一緒にリスクアセスメントを行っております。
是非、ご相談ください。
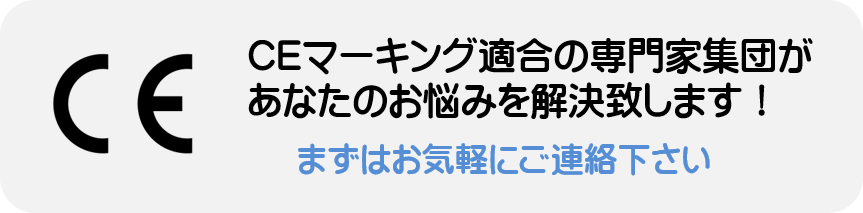